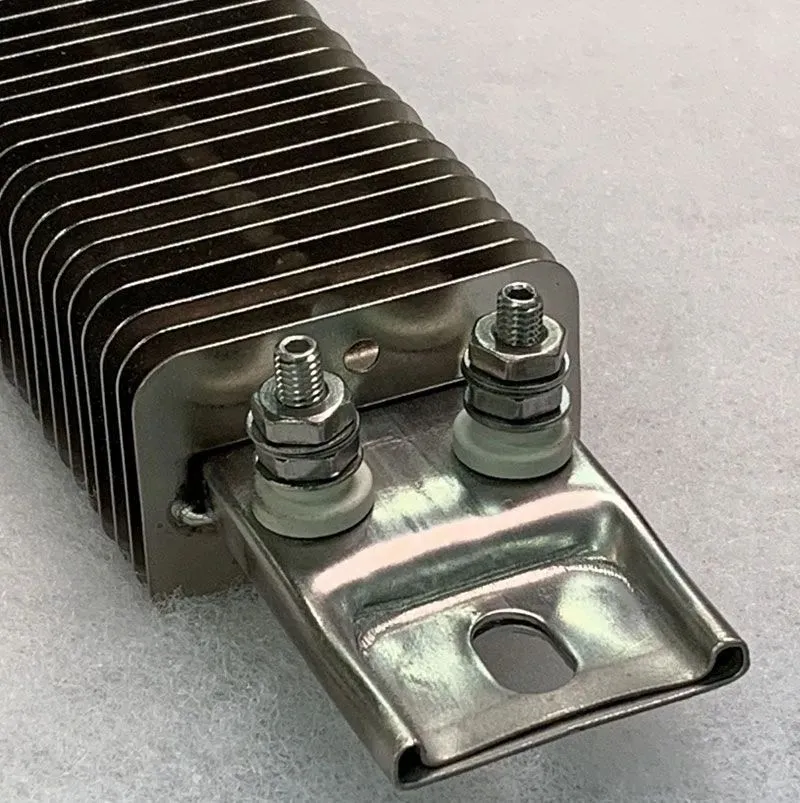
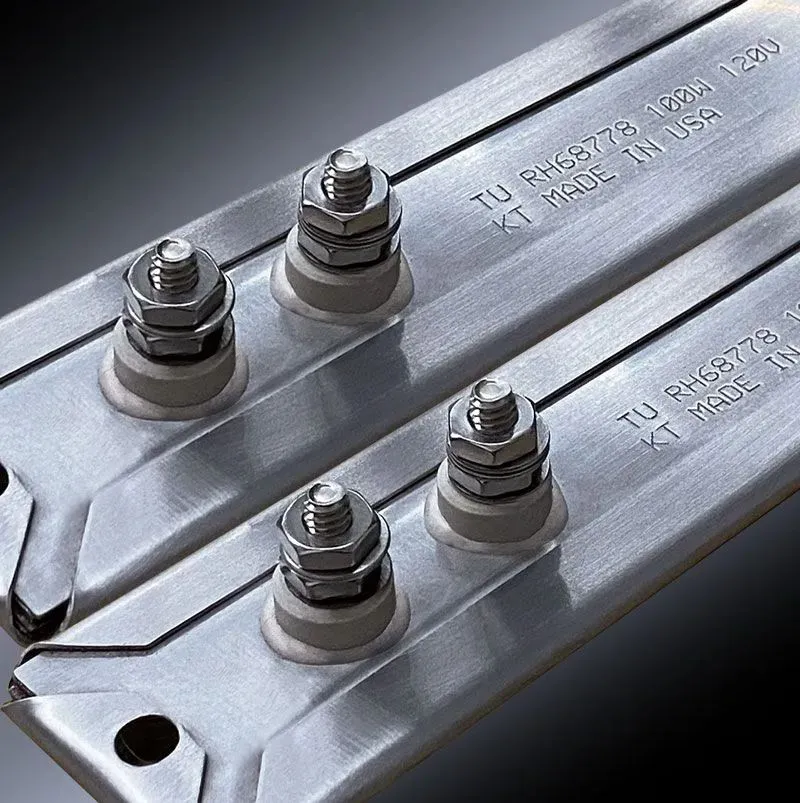
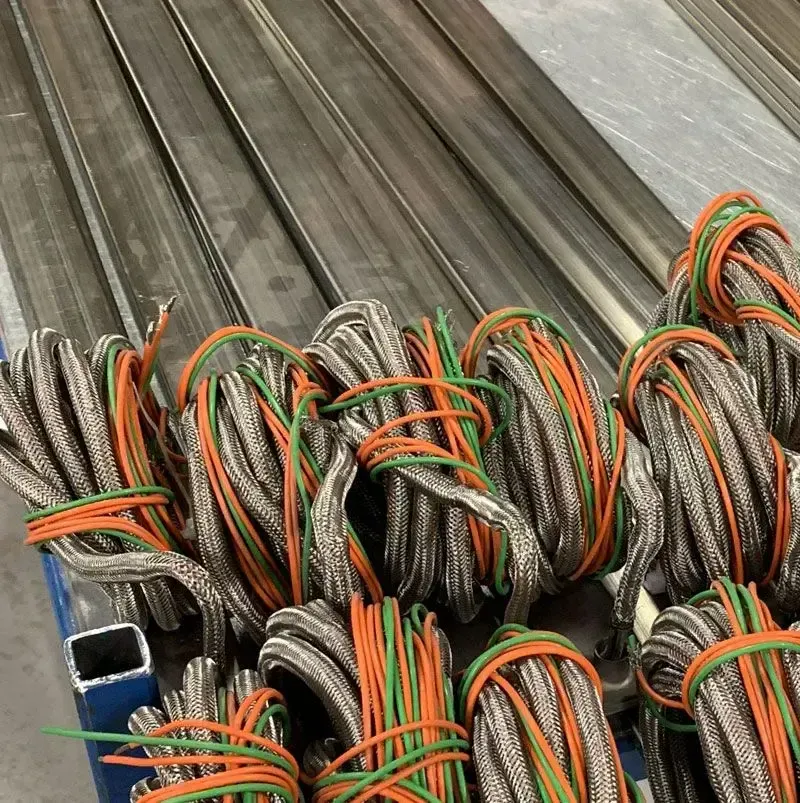
TUTCO CONDUCTIVE
Strip Heaters
TUTCO offers a wide range of customized strip heaters that meet the requirements of a variety of industries. Designed for versatility and reliability, these heaters are ideal for a wide range of uses, including food warming, enclosure heating, and OEM packaging machinery. Our Strip Heater product families include the Ultima, HT Mica, Permaheat, and Ceramic, each delivering exceptional heat transfer and dependable, safe operation. We also offer options for higher watt densities and additional custom features to suit your specific requirements. For detailed application guidance and custom specifications, please contact our factory.
APPLICATIONS
- Platen Heaters
- Compression Molding
- Plastic Pellet Dryers
- Package Sealing
- Sealing Bars
- From Fill Packaging
- Ink Heaters
- Textile Processing
- Chemical Processing
- Laboratory Warmers
- Scientific Testing Equipment
- Food Grade Sealing
- Food Grade Wrapping
- Food Service Warming
- Holding Tanks
- Drum & Barrel Heating
- Incubators/Medical
- Space haters for public transportation
- Road construction equipment (asphalt)
FEATURES
- High temperature capabilities
- Customization options
- Durability
- Custom delivery options
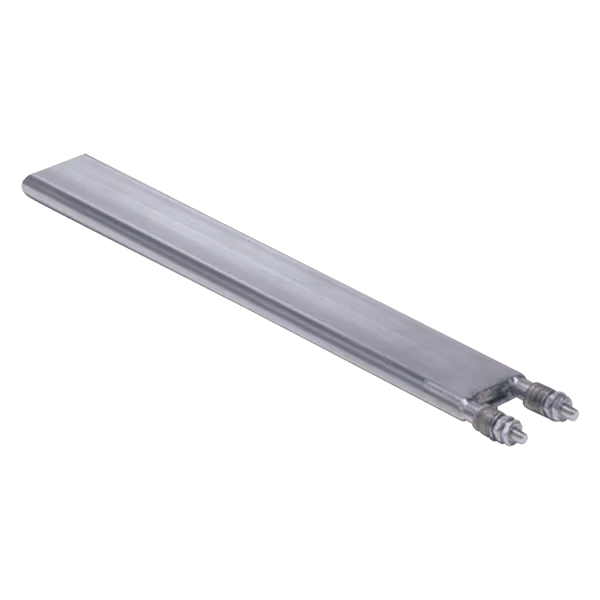