Engineering Insights
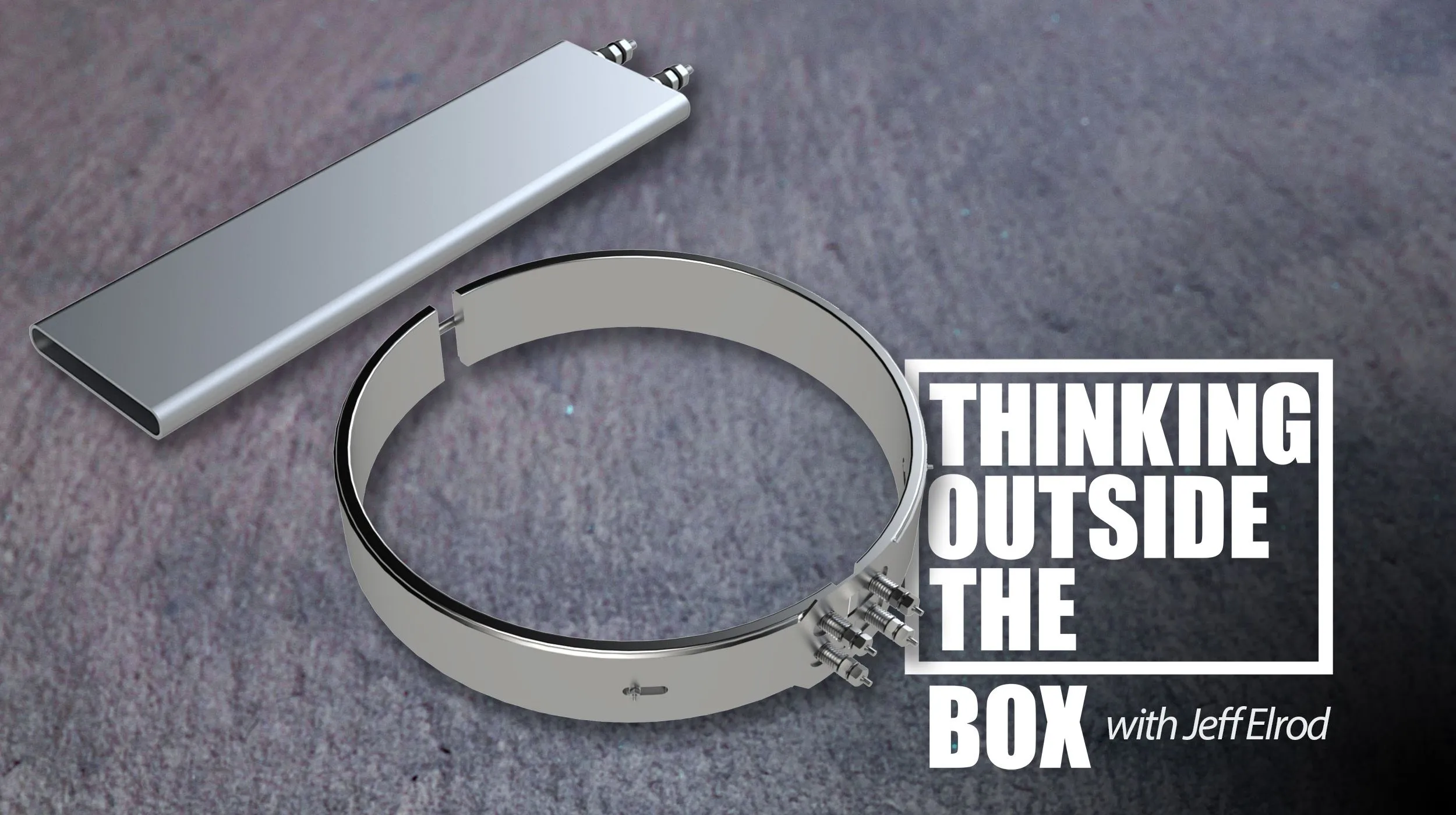
Ultima band and strip heaters deliver a robust selection of band and strip heater options to meet the need of a variety of applications.
Get info 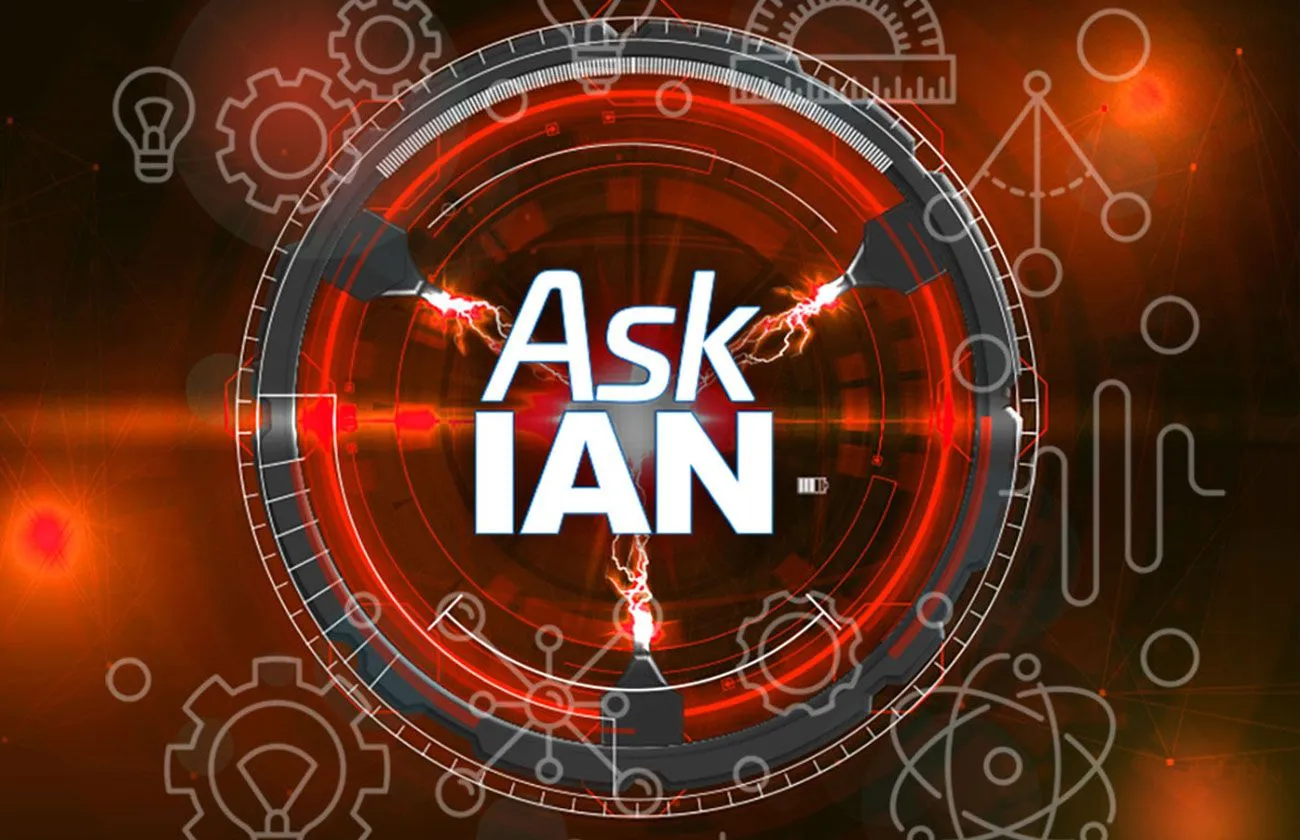
Why select from different insulating materials? The two main factors are temperature rating and water resistance.
Get info 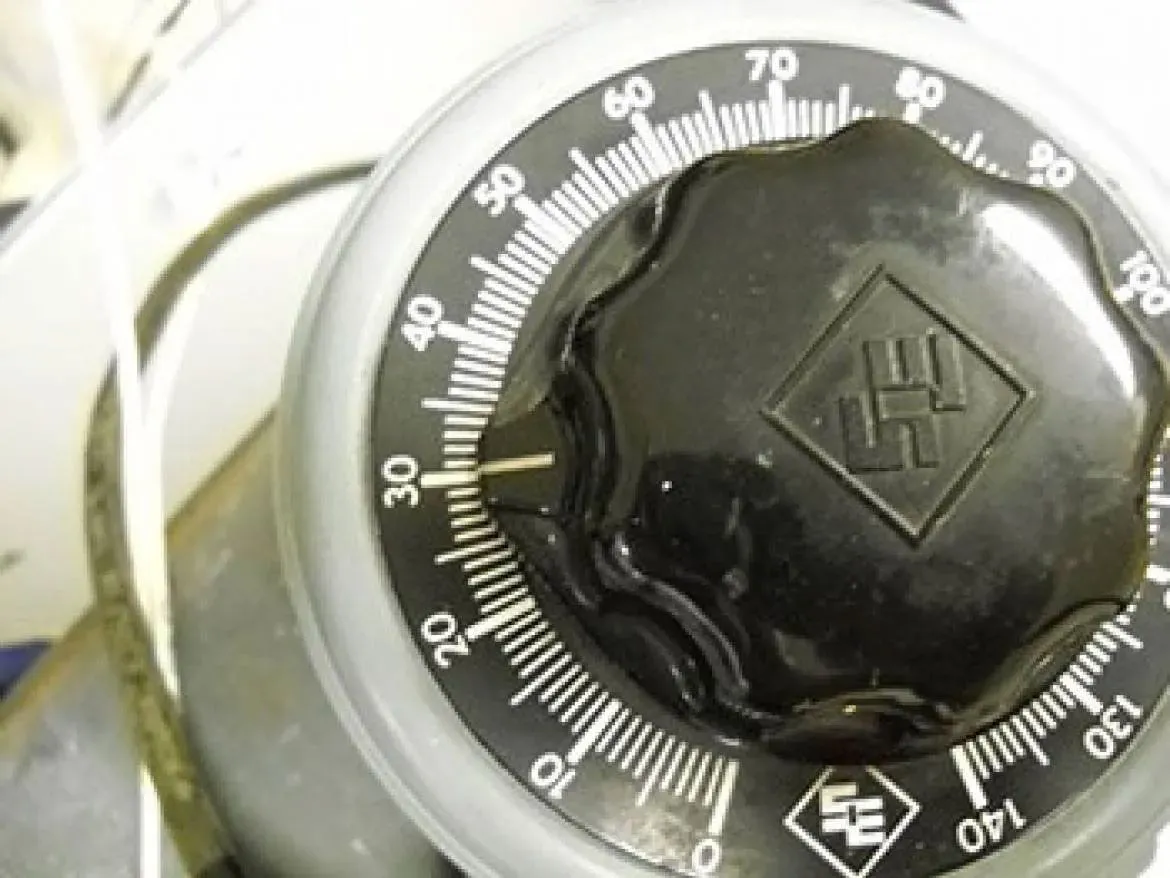
A diode in series with the heating element will reduce the applied energy to the heater for a given voltage and allow a larger lower resistance heating element to be used.
Get info 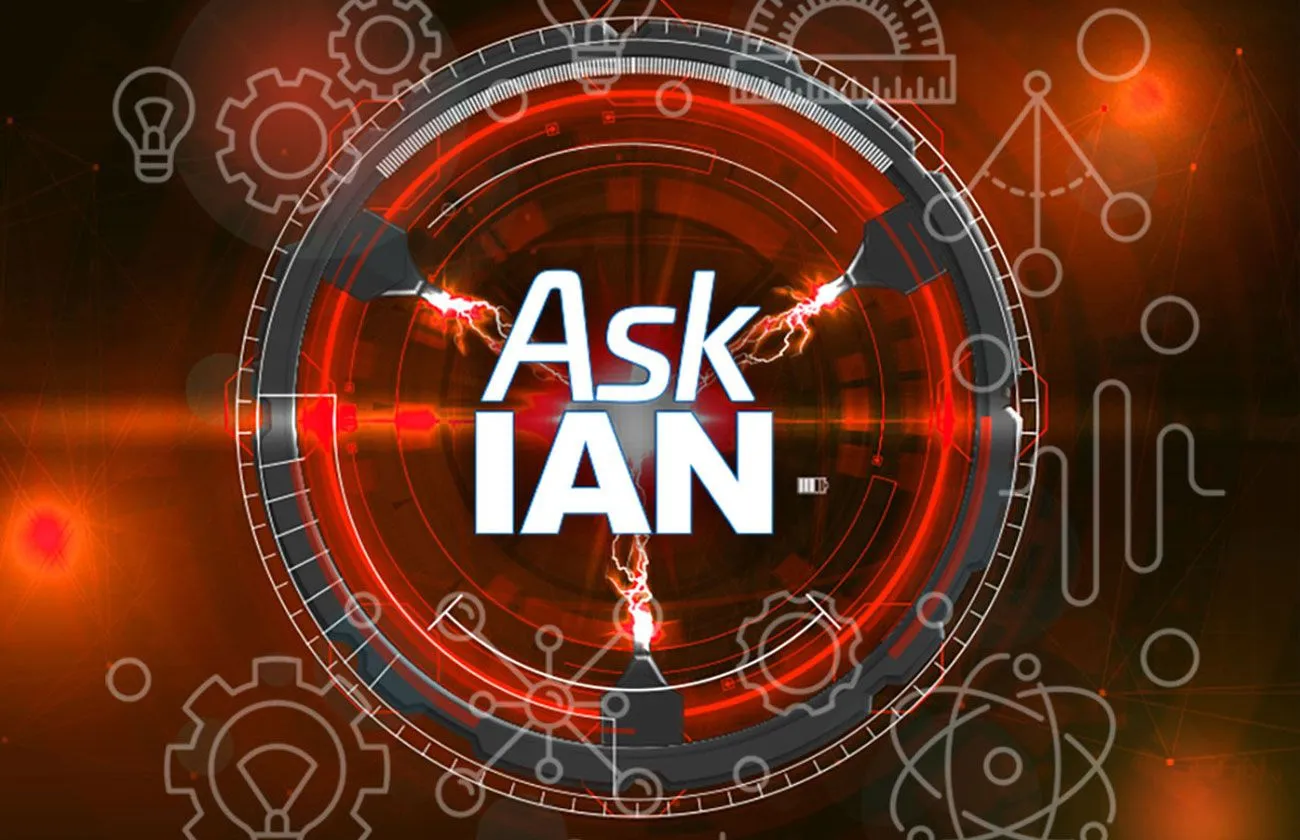
Thermal Expansion is the propensity of solid matter to increase its volume when heated. This change in volume occurs in all directions of an object in length, width, and height.
Get info 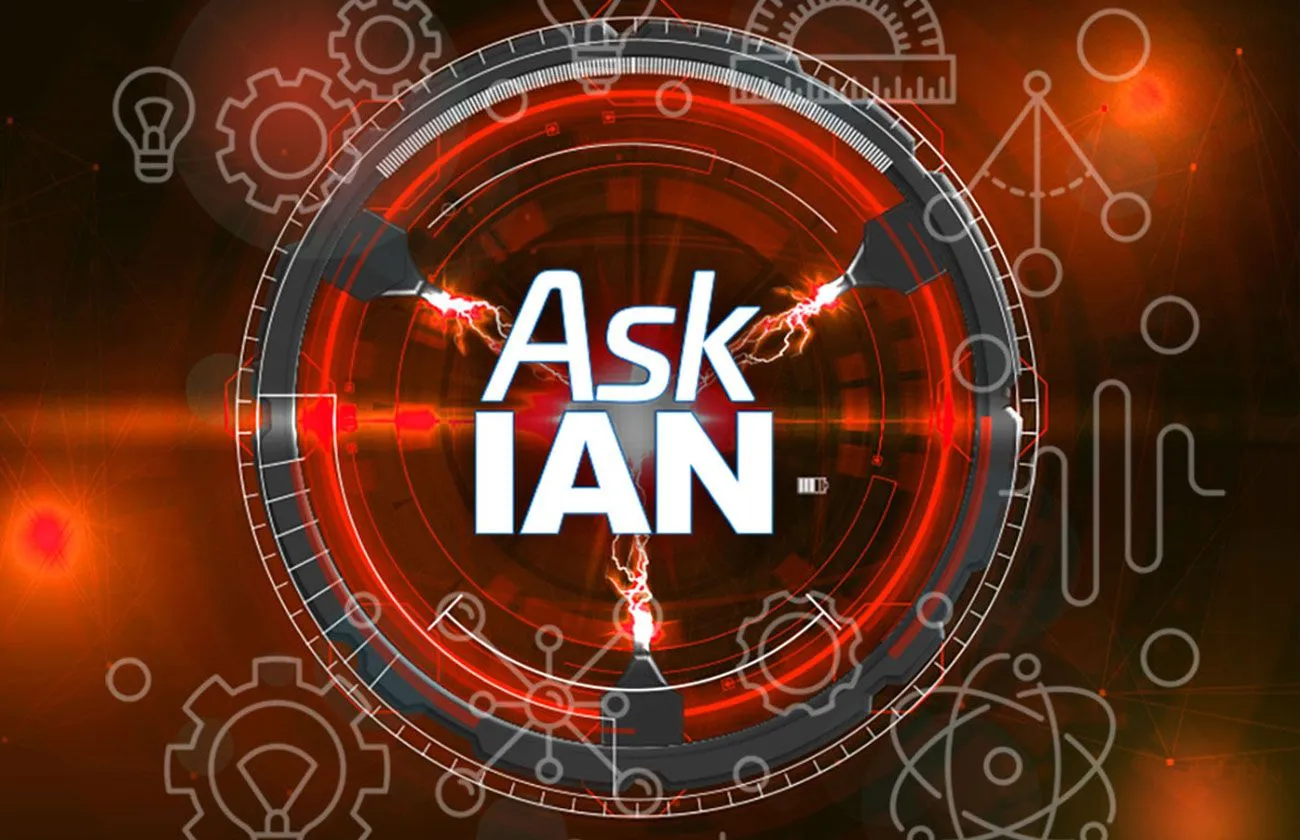
There are many unusual, mostly unknown, and sometimes silly units of measure that exist. Some are used in specific fields of interest, and some are obsolete or too foolish to be taken seriously.
Get info 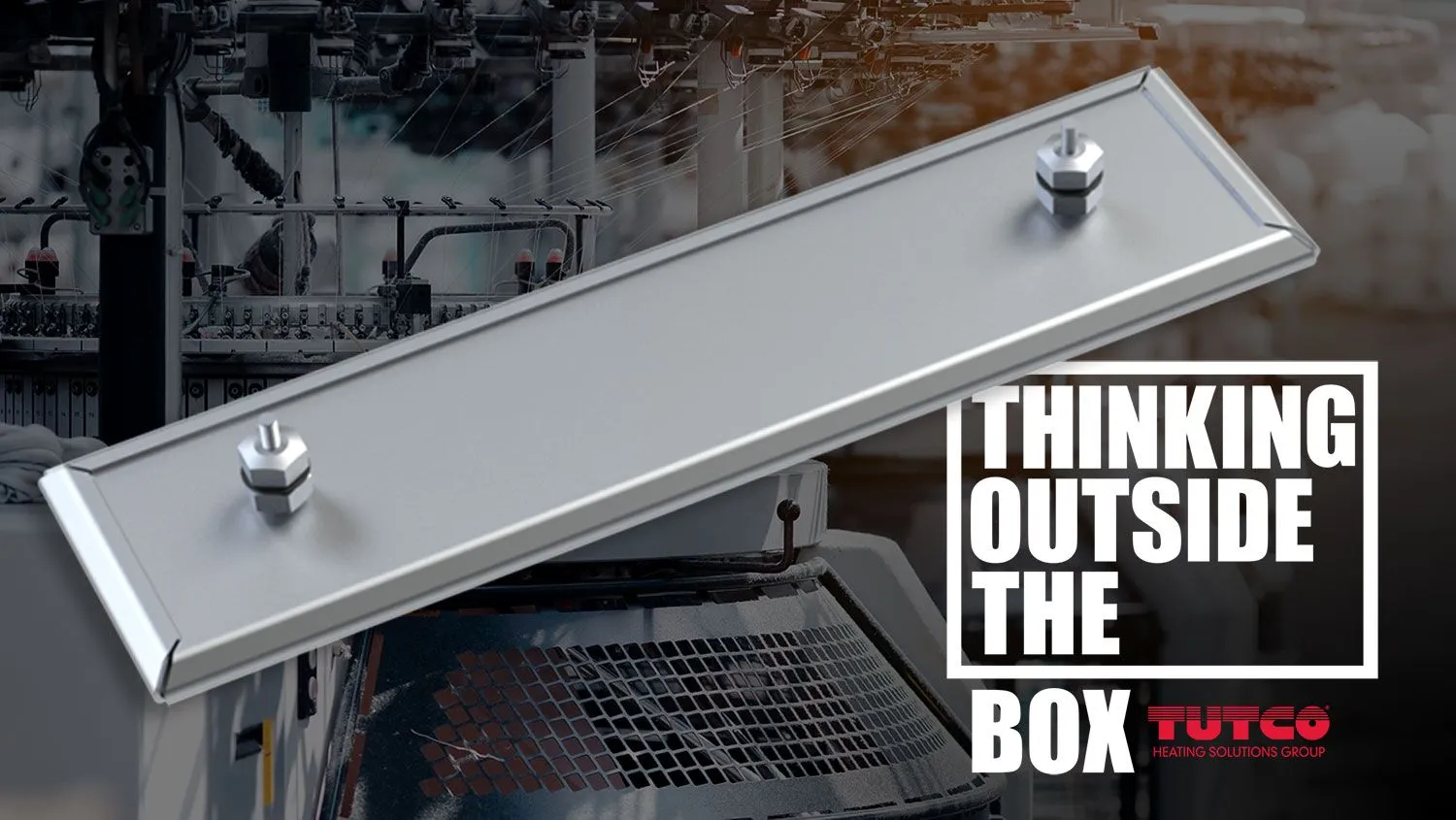
Like their band heater counterparts, HT Mica Strip Heaters can handle temperatures up to 900°F (482°C) and are designed for demanding applications across multiple industries.
Get info 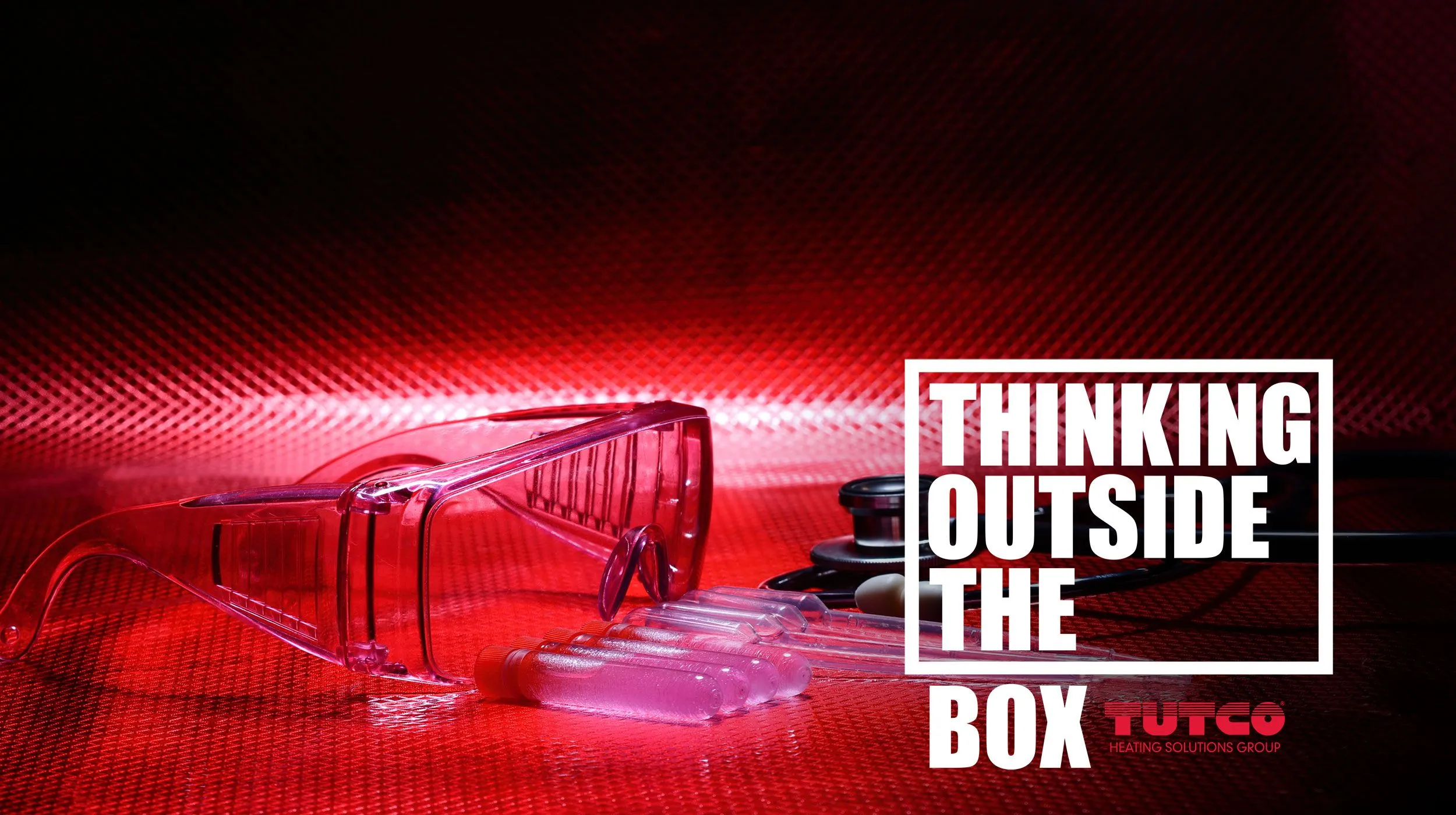
To meet the diverse needs of our customers in the academic and research fields, TUTCO offers a wide range of thermal solutions through our standard product offerings.
Get info